Product Data Management
Accelerate product development
The research, development and design of new products or the re-design of existing ones is the lifeblood of any manufacturing company, but in many cases the design and engineering departments are completely disconnected from the ERP system. What that means is engineers spend a lot of their time answering queries from other areas of the company regarding product status, revision levels, design progress, etc. NetSuite offers a host of native collaboration features that makes this information available on a self-service basis across the organization.
Features
Assembly Items
The Bill Of Materials is established and maintained in NetSuite through the use of assembly items. Using this approach ensures consistency for the user as they create and edit all of the information that is required to effectively manage multi-level BOM structures with minimal effort. Advanced options are available such as the ability to mark items as phantoms, define the expected yield, maintain revisions and/or set effectivity and expiration dates to ensure you always build the right version of your product.
Key Capabilities:
- Multi-Level BOMs
- Phantoms
- Revision Control
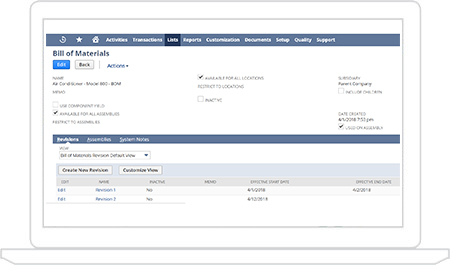
Advanced Bill of Materials
For those companies who want more control over their product data structure, the optional Advanced BOM functionality introduces many additional features. Once enabled, users can create multiple BOM’s for each item—so for example, you can create and maintain separate engineering and production BOMs. Additionally, each BOM can be location-specific or can be linked to multiple end SKUs—ideal where you perhaps sell the same item under multiple brands.
Key Capabilities
- Customizable record structures for complete design control
- Location-specific BOMs
- Link the BOM to multiple end SKUs
- Enhanced Revision control
- Easier integration with PLM systems
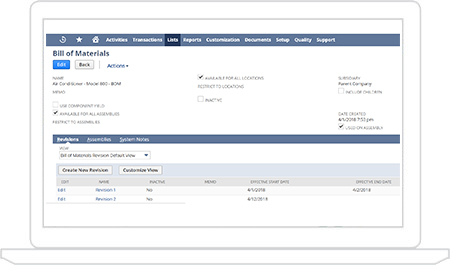
Routings
NetSuite’s routing functionality enables you to easily define the people, machines, work centers and time it takes to make your product. This information when combined with our cost templates determines the expected labor, machine and indirect cost to enable you to track the appropriate level of cost detail from your manufacturing process. When using our Advanced Manufacturing feature, you will also be able to automatically generate a finite capacity schedule by defining additional characteristics unique to your facility. Additionally, our routing functionality can be defined to be location specific where necessary.
- Finite or Infinite Capacity Scheduling
- Location-specific Routings
- Flexible Cost Templates
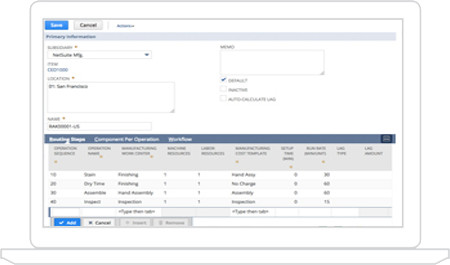
Item Management
NetSuite has a unique approach to item definition where all items start off from the same screen and then the user picks the type of item they want to create. This allows us to present an item definition screen that has been tailored to that specific item type that shows and requires only the information that is necessary. Using our SuiteFlow functionality, we can easily set up automated item numbering, hide or require additional fields, and automate an approval process.
- Quick and Easy Setup
- Mandatory and Custom Fields
- Easy Mass Updating
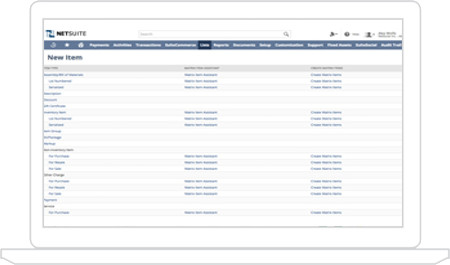
Document Management
NetSuite’s File Cabinet was specifically designed as the central repository for all documents, files and attachments that you need to run your business. Files can be manually uploaded through the system and attached to virtually any record in NetSuite including Customers, Vendors, Orders, etc. By using the optional file drag n drop suitelet, you add the ability to automatically upload and update files by fragging them from your desktop. Files are stored in folders with unique security permissions.
- Securely Stored and Managed
- Captures email attachments
- Cross-reference with NetSuite records
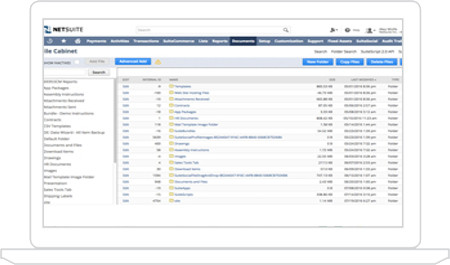
Engineering Change Orders
The Engineering Change Order allows users to capture requested changes, document and share them with all interested parties for approval and then automatically implement them once approved. Change orders can be categorized by type and can update process and documentation changes in addition to material product changes. When used in conjunction with the Quality and Case management features, NetSuite provides complete control over the lifecycle of your products—ensuring that you always plan, manufacture and deliver the current and correct designs.
- Centrally manage all change requests
- Flow proposed changes through SuiteApprovals
- Automatically implement and update all related BOMs after approval
