Supply Chain Planning
Easily balance demand and supply throughout your supply chain using a combination of techniques and strategies
Planning your supply chain is a delicate process of trying to balance demand and supply, potentially across the globe, in a way that provides your company with the right combination of cost control, lead times and service level. NetSuite uses advanced inventory management and demand planning techniques to help you make the right decisions and increase your on time delivery metrics. Each location where you store inventory can be set up with unique parameters to deliver unprecedented control over your supply chain.
Features
Supply Chain Control Tower
NetSuite has been working with customers to understand better how they run and monitor their complex supply chains. The Control Tower Snapshot provides a global time phase view that summarizes your current and future inventory position across our entire global supply chain.
This feature provides the ability to see projected inventory along with any demand or supply that affects it across a time horizon and throughout the supply chain in a way that makes it easy to identify potential issues.
Key Capabilities:
- Actively monitor your inventory, demand and supply across your entire global supply chain
- Time phased view to help identify future imbalances in demand and supply
- Filter results by Subsidiary and Location
- Drill-down into transactions to take action
- Export entire grid to excel for further analysis
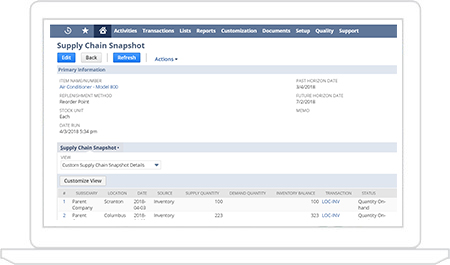
Demand Management
NetSuite’s Demand Planning module offers several ways to calculate and predict demand based on historical demand, open opportunities and/or manually entered or imported sales forecasts. Whether you want the system to review monthly or weekly demand and generate forecasts using moving average, linear regression or seasonal average calculations you will have the ability to review and edit the forecasted demand before proceeding to supply planning. Optionally you can have the system create demand based on sales forecasts.
Key Capabilities:
- Analyze Historical Demand
- Incorporate Sales Forecasts
- Update by CSV Import or web services
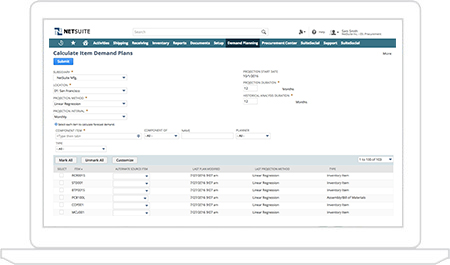
Supply Management
NetSuite’s Demand Planning engine controls the processing of balancing demand and supply. Once demand trends have been evaluated and the plan created, the supply planning process kicks in and tries to generate purchase, work and transfer orders based on the many settings found on the item record. Period of Supply, Lot for Lot and Fixed are amongst the methods used to determine the number and size of the orders generated, while also looking at consumption, time fence and reschedule in/out parameters.
Key Capabilities
- Planned vs Actual Orders
- Multi-Location Supply Planning
- Vendor Management
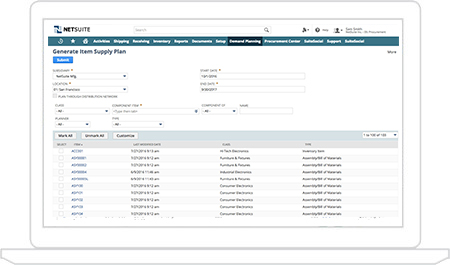